ORBITAL PIPELINE & TUBE WELDING APPLICATIONS OF MAGNATECH TOOLS
01.01.1970Magnatech LLC has dedicated our time to developing pipeline welding systems that work for a variety of industries. The key is quality. Our pipeline welding tools are used even in extreme environments, with temperatures exceeding 120˚F (49˚C) or dropping to -40˚F (-40˚C). From Aerospace welding to sanitary welding required for the pharmaceutical and food industries, we provide all the systems you need to meet guidelines and pass inspection.
Aerospace Industry
WELDING SYSTEMS FOR GAS TURBINES AND ROCKET ENGINE COMPONENTS
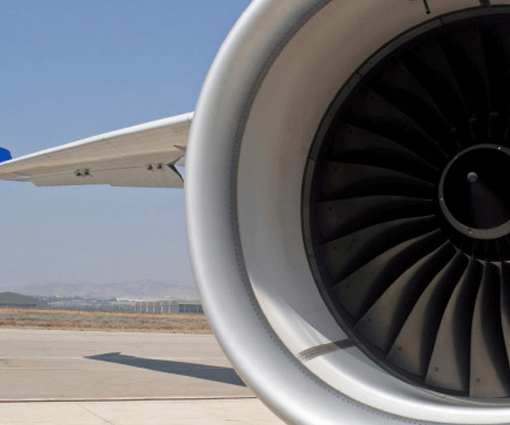
The aerospace industry was the first to recognize the necessity for automated orbital welding. Critical fuel and hydraulic control lines are exposed to extreme cyclical mechanical and thermal stresses. This led to a search for a more reliable joining technology to replace mechanical fittings. For over four decades, we have provided specialized automated orbital welding systems to manufacturers and component suppliers for turbine engine fabrication. Orbital welding is a key technology used by specialized providers of aerospace welding services for component repair and overhaul.
Currently, a single aircraft's high-pressure systems can contain more than 1,500 joints. All of these joints have been welded using automated orbital welding equipment. The precise control of heat input by orbital welding is critical to prevent distortion.
- Digital control of the welding process ensures perfect, repeatable welds required by aerospace welding standards.
- Magnatech orbital welders incorporate weld monitoring and QC reporting for each weld made.
- Autoprogramming automatically generates weld parameters, simplifying operator training
Magnatech serves the aerospace welding industry with a range of models and capabilities. We provide operator training, timely service and technical assistance to our customers worldwide.
Food and Beverage Industry
SANITARY WELDING SYSTEMS THAT MEET FOOD AND BEVERAGE INDUSTRY REQUIREMENTS
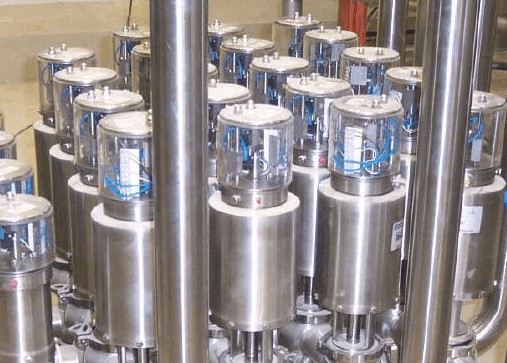
Magnatech is a leading provider of orbital tube welding systems that allow the food and beverage industries to meet the strict hygienic requirements required of sanitary tubing. Automated orbital welding is increasingly being used by contractors and fabricators for the job of welding sanitary process tubing. These industries require consistent, full penetration welding. The industry move to use Clean in Place (CIP) technology and the new ASME BPE (Bioprocessing Equipment) standard has increased the demand for automatic tube welding in these industries. Magnatech is here to meet those demands. Since 1970 we have provided expertise in the area of orbital welding, and are committed to providing food, beverage and dairy reliable and cost-effective welding solutions.
Magnatech food and beverage welding systems set a standard for the industry. We manufacture automated orbital welding systems used in the food, dairy and beverage industries around the world, and invite you to learn more about our products and services.
- Our EZ Orbital System provides a cost effective tool designed specifically for this market
- Models are available for fusion only (open and closed arc) and with wire feed capability
- Magnatech is always available as a technical resource and for technical assistance.
The food, dairy and beverage industries must meet sanitary process welding standards. Allow us to show you how orbital welding will improve your sanitary welding consistence and quality, while reducing fabrication and installation time.
Fossil Fuel Power Generation Industry
ORBITAL WELD HEADS DELIVER CODE WELDS AND HIGHER PRODUCTIVITY EVEN WITH TIGHT RADIAL CLEARANCES
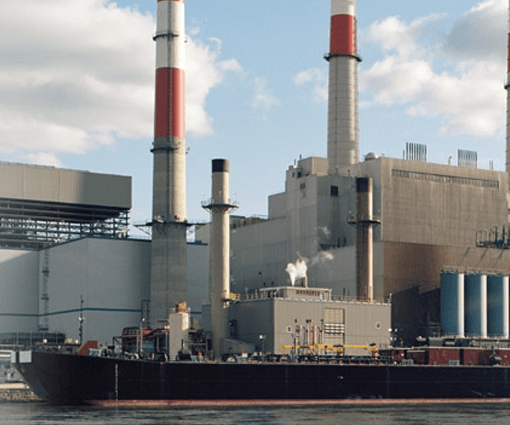
Our orbital welding systems have long been used in the fossil fuel power generation industry. Pipe and tube welding in the electric power generation industry has greatly influenced the development of automated orbital pipe welding. A common consideration at power plants is that welds must be made in areas with limited space – tight axial and radial clearance for both initial construction and subsequent maintenance. Magnatech's engineering staff has met these challenges with compact weld heads for multipass welding – capable of operation in the rugged environment of a power plant during a maintenance outage.
- Our compact orbital weld heads are used in fabrication of tubular superheaters, reheaters, and economizer assemblies.
- Weld Heads are designed to withstand multipass welding on tube and pipe materials requiring high preheat temperatures.
- Magnatech is the first to provide Autoprogram Generation for multipass pipe welding.
- Position-based programming allows up to five continuous passes to be welded – no need to stop after each pass.
Magnatech has proven solutions for component fabrication, construction, and power plant maintenance ranging from small diameter boiler tube welding to heavy wall diameter headers. We provide technical specialists for field training at the fab shop or job site.
Nuclear Power Generation
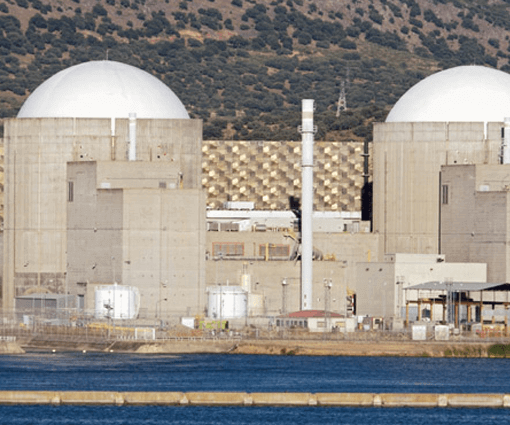
Orbital pipe and tube welding has been used in the nuclear power generation industry since the very first commercial plants were built. Fabricators and contractors demand the consistent code-quality welds and the ability to ensure that welds are made precisely within the parameters defined by the WPS/PQR. With every weld undergoing testing, the disruption to schedules for repairs and cut-outs is unacceptable. Automated orbital welding eliminates the variability of manual welding. Heat input, an important parameter for many nuclear pipe welding applications, can be precisely controlled and monitored; which is difficult to accomplish with manual welding.
Magnatech has provided both standard and modified equipment equipped with video arc monitoring for nuclear maintenance applications
The higher duty cycle of automated orbital pipe welding reduces construction time, and allows contractors to meet the tight deadlines for work required during plant shutdowns. Our tube welding systems are used by nuclear welding contractors for small diameter instrumentation line installation.
- Long history of use for nuclear pipe welding in PWR, BWR, and CANDU design reactors
- Video Arc Monitoring Systems for nuclear pipe welding in high radiation areas
- Power sources engineered for data logging welding parameters.
Offshore Oil and Gas Production
MECHANIZED WELDING SOLUTIONS FOR OFFSHORE OIL AND GAS PRODUCTION
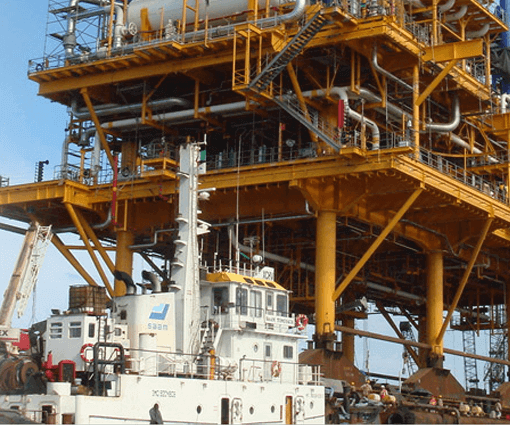
Exploration for new oil and gas fields is increasingly moving offshore. The wide range of applications, with welds often subjected to extreme environments, put a high demand on weld quality. Magnatech equipment has been used extensively for offshore pipeline welding projects using the GTAW and FCAW processes.
Many gas and oil fields contain high levels of dangerous and corrosive hydrogen sulfide and carbon dioxide. Special CRA (Corrosion Resistant Alloy) clad pipes are used to withstand corrosion, and require special welding techniques. Multi-billion dollar pipelines have been destroyed in months if the welding is not properly performed. Magnatech pipeline welding systems offer a proven solution.
Magnatech provides solutions for the welding of small diameter, heavy wall Duplex stainless steel pipes used for control of sea floor well components.
The gigantic platforms that are used for both drilling and production are constructed of large diameter tubular assemblies. Fabricators use Magnatech's Pipeliner system, with its high deposition rate FCAW process for welding of the legs, known as "jackets". The "topsides" platform equipment and process piping are welded by fabricators worldwide using Magnatech orbital welding systems.
- Specialized pipeline welding systems for offshore welding
- Proven solutions and technical expertise in welding CRA clad piping
- Magnatech provides operator training and assistance developing weld procedures worldwide.
With growing energy demand globally, the technology to extract offshore oil and gas in ever deeper waters demands the weld integrity that automated orbital welding can uniquely provide.
Pharmaceutical & Biotechnology Industry
MAGNATECH'S HYGIENIC WELDS FOR THE PHARMACEUTICAL INDUSTRY
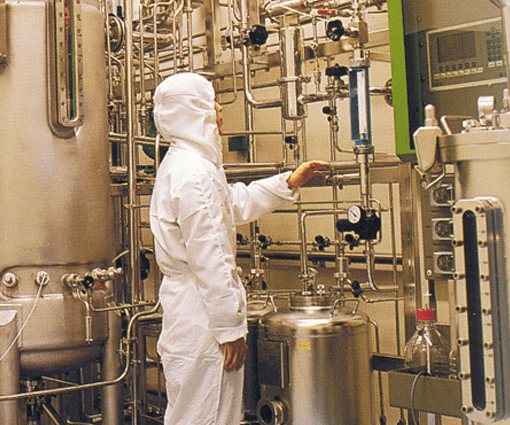
Orbital tube welding has proven to be a most effective method when it comes to generating crevice-free welds that are essential for controlling growth of microorganisms in hygienic process and fluid delivery systems. The ASME Bioprocessing Equipment (BPE) Standard states that welding on tubing shall be performed using automatic (machine) welding techniques, such as orbital tube welding.
High purity industries include pharmaceutical and biotechnology and they have a particular need for both cleanliness and cleanability in their piping systems. This is especially important for CIP (Clean in Place) systems.
Magnatech orbital tube welding systems are used for fusion welding by fabricators of the many high-purity process piping subsystems of pharmaceutical or vaccine production facilities, such as sterile "Water For Injection" (WFI) systems.
Magnatech orbital welding systems are used on high purity process piping due to their repeatability. Because of the impracticality of radiographic and ultrasonic inspection on small diameter tubing, other quality control methods must be employed such as weld coupon examination. The Tubemaster provides weld monitoring/QC data for every weld.
- Digital control of the orbital tube welding process ensures perfect, repeatable welds required by ASME BPE welding standards.
- Magnatech orbital welders incorporate weld monitoring and QC reporting for each weld made.
- Autoprogramming automatically generates weld parameters, simplifying operator training.
Magnatech serves the pharmaceutical and bioprocess industries with a range of models and capabilities. We provide operator training, timely service and technical assistance to our customers worldwide.
Petrochemical
Automated orbital welding systems for Petrochemical and Chemical Plants
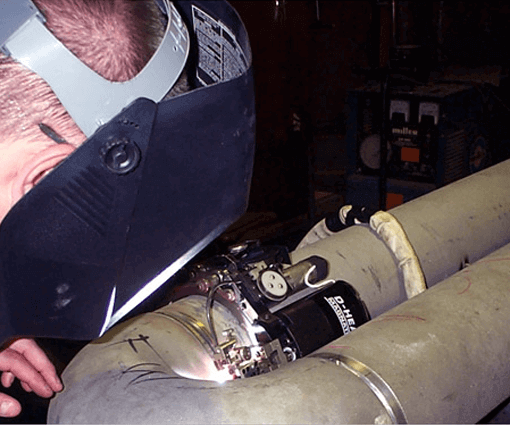
If there is one thing a chemical plant has in abundance it is tubes and pipes ranging in size from small to large diameters, and from standard carbon and stainless alloys to highly exotic custom-formulated alloys that require exacting weld procedures. Magnatech has a wide range of automated orbital welding systems. Whether your application calls for welding small diameter, thin wall instrumentation tubing or large diameter, heavy wall high pressure piping, we have an orbital solution.
Many manufacturing processes requires special alloy pipe; whether the need is to provide corrosion resistance or to withstand operation at high temperatures while maintaining ductility and creep strength. Automated orbital welding minimizes and precisely controls heat input, which is often critical to maintain the properties of these special alloys.
Maintenance welding can mean interrupting the operation of a large facility, resulting in profit losses by the hour. The high duty cycle of automated orbital welding minimizes the time required for maintenance operations by cutting weld time and virtually eliminating repairs.
- Our compact orbital weld heads allow pipe welding in areas with very limited space and accessibility, a common situation in maintenance..
- Weld Heads are designed to withstand multipass welding on tube and pipe materials requiring high preheat temperatures.
- Magnatech is the first to provide Autoprogram Generation for multipass pipe welding.
Magnatech has proven solutions for petrochemical component fabrication, construction, and maintenance. We provide technical specialists for field training at the fab shop or job site.
Process Piping
MAGNATECH ORBITAL PIPE WELDING SYSTEMS ALLOW CONTRACTORS TO CONSISTENTLY MEET ASME B31.3 CODE STANDARDS
Mechanized Welding Systems for Gas and Water Pipelines
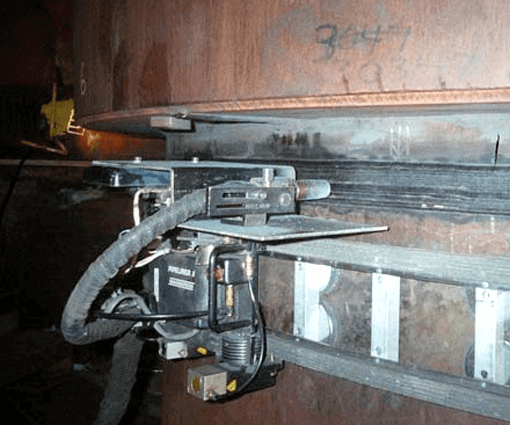
Process piping covers the complete spectrum in terms of pipe size, wall thickness and alloy. Magnatech's automated orbital welding systems are used in a number of diverse industries. These include companies manufacturing consumer products such as cosmetics and detergents; companies erecting oil process plants where water and impurities are removed before oil is pumped down a pipeline; and fabricators and installers of industrial air conditioning and heating systems.
Water treatment facilities, whether for the treatment of potable water or wastewater, require extensive pipe welding for new construction and maintenance. This work is often carried out within the constraining confines of service tunnels.
- Precise machine control of the welding process necessary for welding alloys used for corrosion and temperature resistance.
- Allows lower skilled welders to make welds meeting industrial piping code standards.
- The high productivity and elimination of repairs shortens maintenance shutdowns.
- Magnatech's orbital welding systems provide Autoprogram Generation for multipass process piping welding.
Magnatech offers welder training anywhere in the world and assistance in developing weld procedures. Let us demonstrate the productivity and ease of use of automated orbital welding of your process piping.
Semiconductor Industry
ORBITAL TUBE WELDING SOLUTIONS FOR HIGH PURITY GAS DELIVERY APPLICATIONS
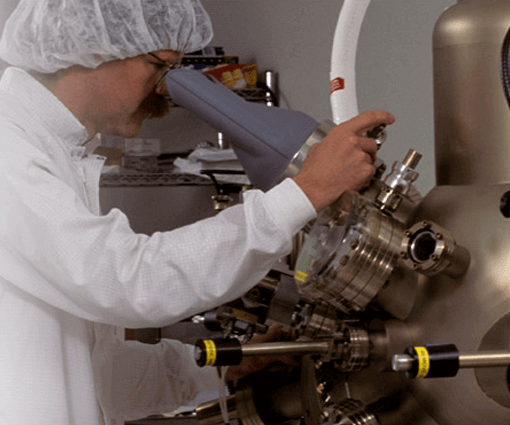
Since the early 1980's, autogenous orbital GTAW welding has been utilized for joining the high purity gas delivery and process piping in the semiconductor and related industries.
A semiconductor fabrication facility contains miles of stainless process lines transporting the gases used in chip manufacturing. These gases may be highly toxic and highly corrosive. The high degree of weld integrity required is only achieved by orbital GTAW welding. Most semiconductor welding is done using weld Heads which fully enclose the joint, ensuring superior gas coverage and minimized any oxidation of the weld bead. Wall thickness and tube material generally allows fusion welding to be done in a single pass, without added filler wire. The introduction of the SEMI F 78-0304 standard in the early 1990's provided a comprehensive guideline for orbital GTAW use by specialist contractors.
- Magnatech orbital equipment is user-friendly - easy to program and use.
- Magnatech's 800 Series Heads incorporate all controls on the weld head for practical operation away from the power source.
- Digital technology eliminates the need for periodic weld head calibration – providing the repeatability mandated by the semiconductor welding industry.
Magnatech power sources incorporate integral weld monitoring software, which provides immediate QC data and ensures that every fusion weld is made within defined acceptance criteria limits. Let Magnatech demonstrate what set us apart in equipment ease of use, reliability, with worldwide training and service.
Orbital welding of the predominant 0.25" - 0.50" (6.3 - 12.7mm) tube sizes has become routine to meet the stringent standards in the industry. Recently, the application of orbital tube welding has expanded to the welding of non-critical, gas exhaust and environmental gas purge lines for the new 450 mm wafer processing tools, requiring orbital welding of up to 8" lines.
Shipbuilding Industry
ORBITAL WELDING SOLUTIONS FOR CRITICAL SHIPBOARD PIPING ON COMMERCIAL AND NAVAL VESSELS
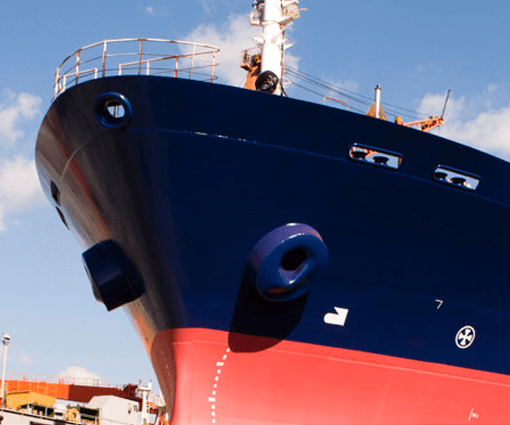
Commercial and naval ships have extensive pipe work for numerous critical subsystems: from power to fuel and water. Pipe welding, whether for construction or maintenance, is often done in cramped conditions with minimal clearances. Magnatech's compact weld heads allow multipass pipe welding producing welds meeting any code standard.
Our pipe welding systems are in daily use in the rugged environment of a shipyard. Copper nickel pipe material, frequently used in ships, is difficult to weld manually, but readily welded by automated orbital systems. The nuclear power plants of U.S. Navy ships require critical welds in stainless, high nickel, and titanium materials. Orbital welding is extensively used by shipyards for new construction, and by naval bases for maintenance and modification.
- Our compact orbital weld Heads are used in shipbuilding and maintenance worldwide.
- Welding systems are designed for multipass pipe and tube welding.
- Magnatech orbital welders use position-based programming, allowing up to five continuous passes – no need to stop after each pass.
- Magnatech is the first to provide Autoprogram Generation for multipass pipe welding. Compact, lightweight power sources facilitate orbital pipe welding below deck.
Magnatech has proven pipe welding solutions for the shipbuilding industry. Learn more about these solutions and how they can benefit your shipbuilding efforts.
Water and Gas Pipeline Industries
MECHANIZED WELDING SYSTEMS FOR GAS AND WATER CRA-CLAD PIPELINES
Mechanized Welding Systems for Gas and Water Pipelines
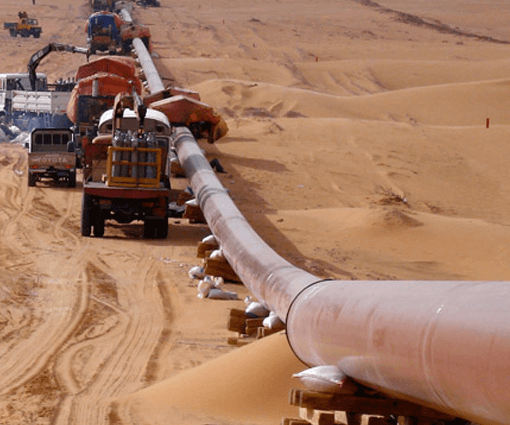
Welding cross country oil and gas pipelines along with water pipelines is one of the most demanding tasks in mechanized welding. Magnatech's welding systems are in daily use in desert conditions in Saudi Arabia, where blowing winds are a constant and temperatures reach 120˚F (49˚C) and higher. They are also used in harsh winter conditions in Canada, where temperatures drop to -40˚F (-40˚C). Because only one pipe length can be added at a time to the existing line, equipment reliability is paramount in joints-per-day productivity.
- Many gas and oil fields contain high levels of dangerous and corrosive hydrogen sulfide and carbon dioxide. Special CRA (Corrosion Resistant Alloy) clad pipes are used to withstand corrosion, and require special welding techniques. Multi-billion dollar pipelines have been destroyed in months if the welding is not properly performed. Magnatech pipeline welding systems offer a proven solution.
- Magnatech's pipeline welding systems can be used on pipe from 6" (168mm) to 72" (1830mm) using standard Guide Rings (mounting bands) and to any larger diameter using Flx-Track.
- Uphill mechanized welding is a very forgiving and easy-to-use process, virtually eliminating repairs, and allows operation by lower-skilled welders.
- Our pipeline welding systems use a unique Push-Pull or floor-mounted Push wire feeders that removes the wire spool from the weld head, allowing the use of standard economical 15 kg (30 lb.) spools. The lightweight heads are easier for welders handling during installation.
- Magnatech offers welder training anywhere in the world, assistance in developing weld procedures, and long term support when required. Magnatech has a proven track record of successful pipeline welding projects.
Pipeline welding calls for the very best mechanized welding systems and support, and Magnatech is up to the task.
More Orbital Welding Applications
ORBITAL WELDING SOLUTIONS FOR ANY TUBE AND PIPE WELDING CHALLENGE
We develop unique solutions for water pump lines in deep shaft mines, large HVAC systems, flexible metal hoses, and more!
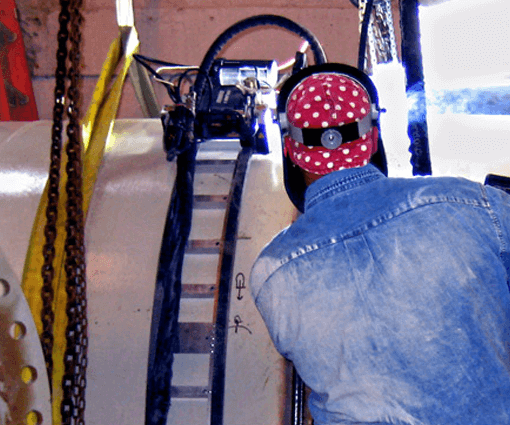
Many potential applications for orbital welding fall outside standard categories. Manufacturing often must weld pipe and circular workpieces to high quality standards.
Maintenance may require weld overlay buildup to replace metal lost due to corrosion and erosion on circular OD's and ID's of round components. Mechanized welding is ideal for these tasks which may require many hours of continuous welding. The high duty cycle of automated welding significantly reduces both project time and costs.
Unique Welding Solutions
Custom welding solutions designed for unique projects
IF A STANDARD ORBITAL SYSTEM WON’T WORK, MAGNATECH’ S EXPERIENCED ENGINEERING GROUP CAN DESIGN A UNIQUE SOLUTION
Magnatech has engineered hundreds of custom design solutions over forty years.
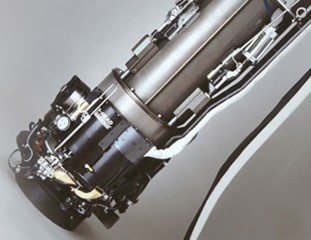
There are many pipe and tube welding applications for which a standard Magnatech LLC system cannot be used. Spatial constraints, workpiece geometry, and proposed use of equipment in hazardous conditions requiring remote operation are but a few of the reasons custom engineering may be required.
Magnatech LLC has engineered hundreds of custom design solutions since our business was founded in 1946. Often, minor changes to weld head design, electronic controls and software are all that is required. Other challenges involve the engineering of an entirely new system with specialized accessories.
The construction and maintenance of nuclear power plants dictates the need for unique pipe welding. An example is the need for remotely controlled welding, where manual welders have limited access due to radiation levels. The weld heads may be required to be located and mounted by remotely operable devices. Video Arc Monitoring systems incorporating miniature video cameras with special filtering allow an operator to view the workpiece before welding to observe fit up; monitor the weld puddle during welding; and visually inspect the completed weld.
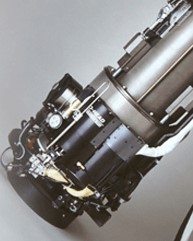
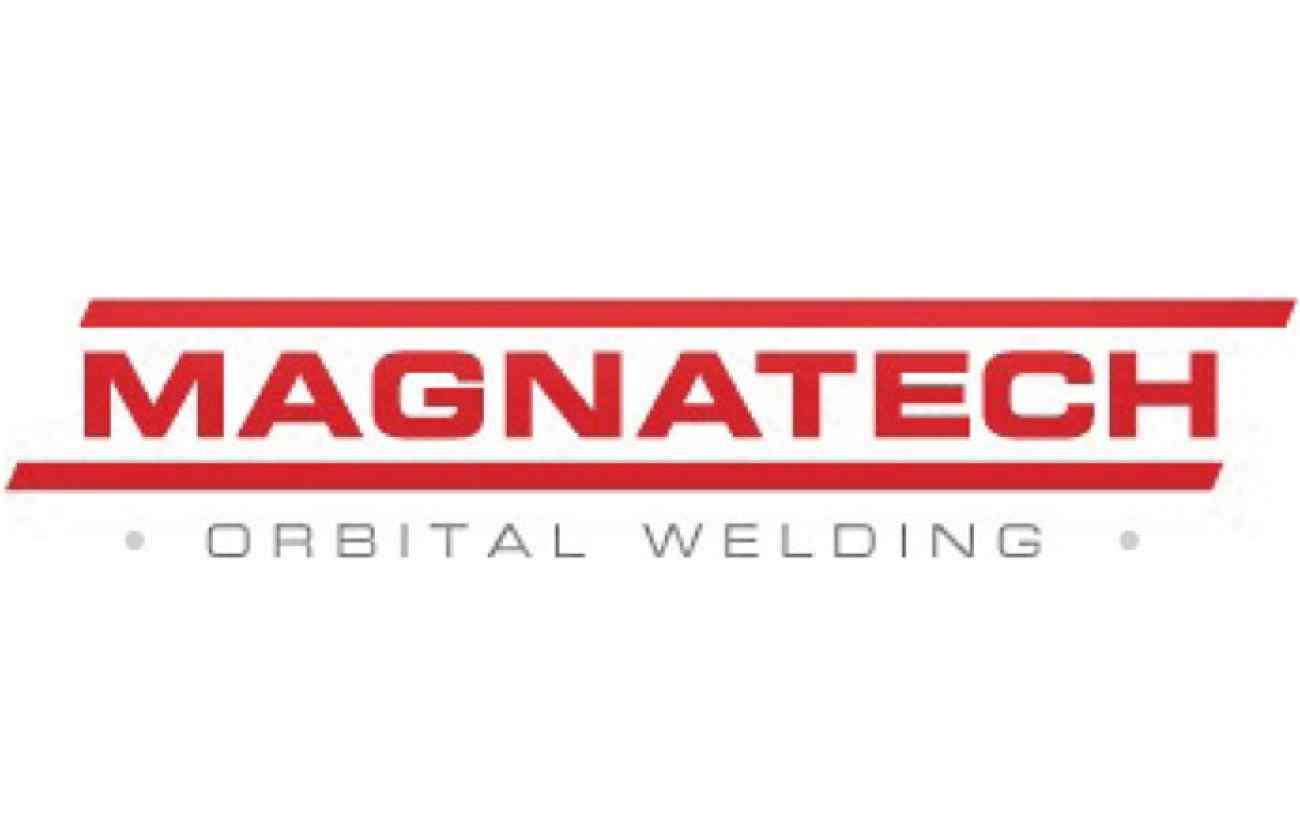
More about Magnatech
Magnatech´s mission is to provide orbital welding solutions for tube and pipe applications. We design our orbital welding equipment to be reliable, simple and productive. Please contact us to discuss your specific application and to learn how orbital welding can improve your working day!